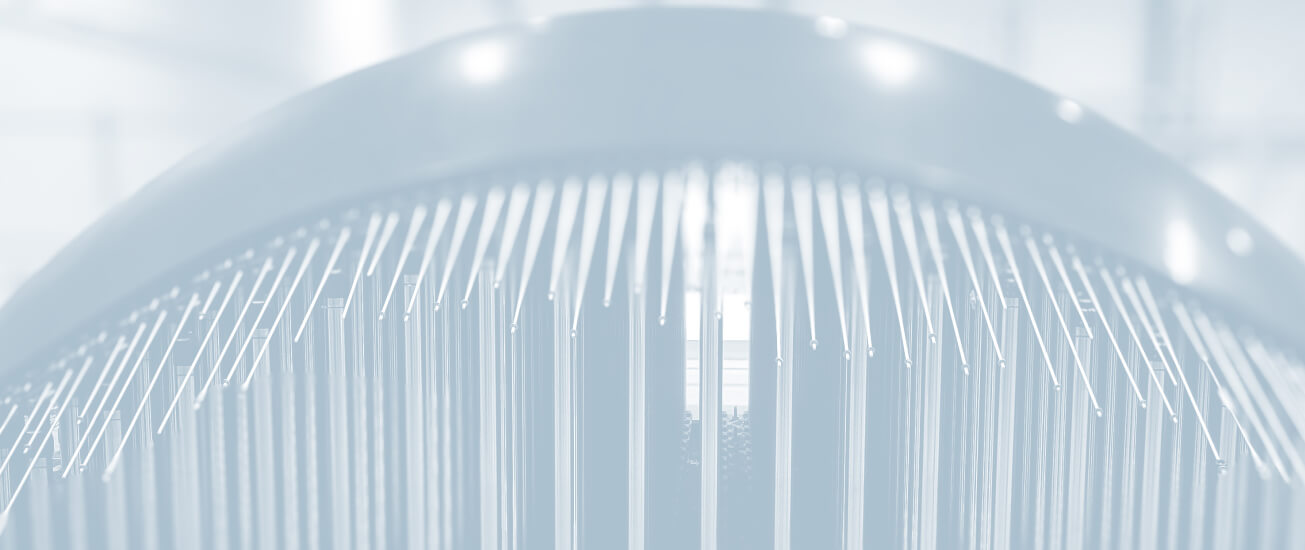
Services Sectors
The most innovative way to curve composite material.
Mission Statement
We lower barriers for companies to implement bespoke shapes and solutions using innovative materials, digital automation, and the latest technologies.
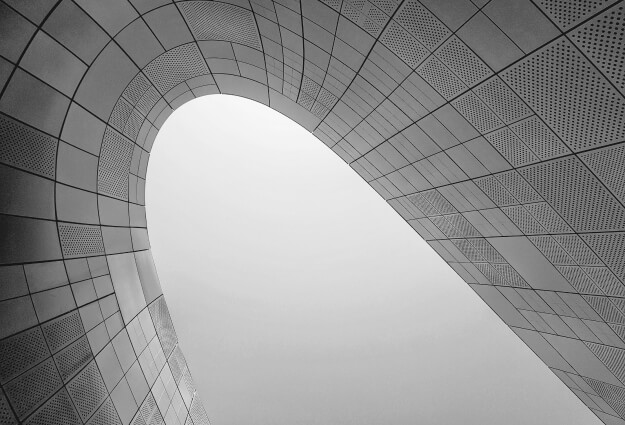
Technology
Our reconfigurable system creates your CAD file shape in minutes. Our adaptive molding system uses a membrane on top of digitally-controlled actuators to produce smooth singly- and doubly-curved surfaces on which we thermoform, mold, and cure a wide range of materials.
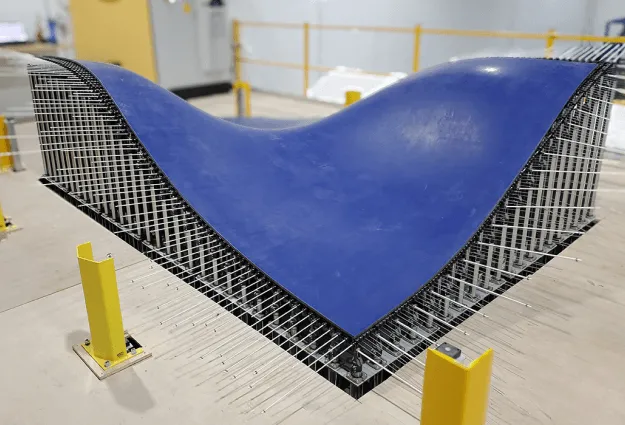
Our Collaborators
At bespline, we consider our suppliers and clients like collaborators to enable, together, what previously wasn’t possible, affordable, or sustainable.
.png)
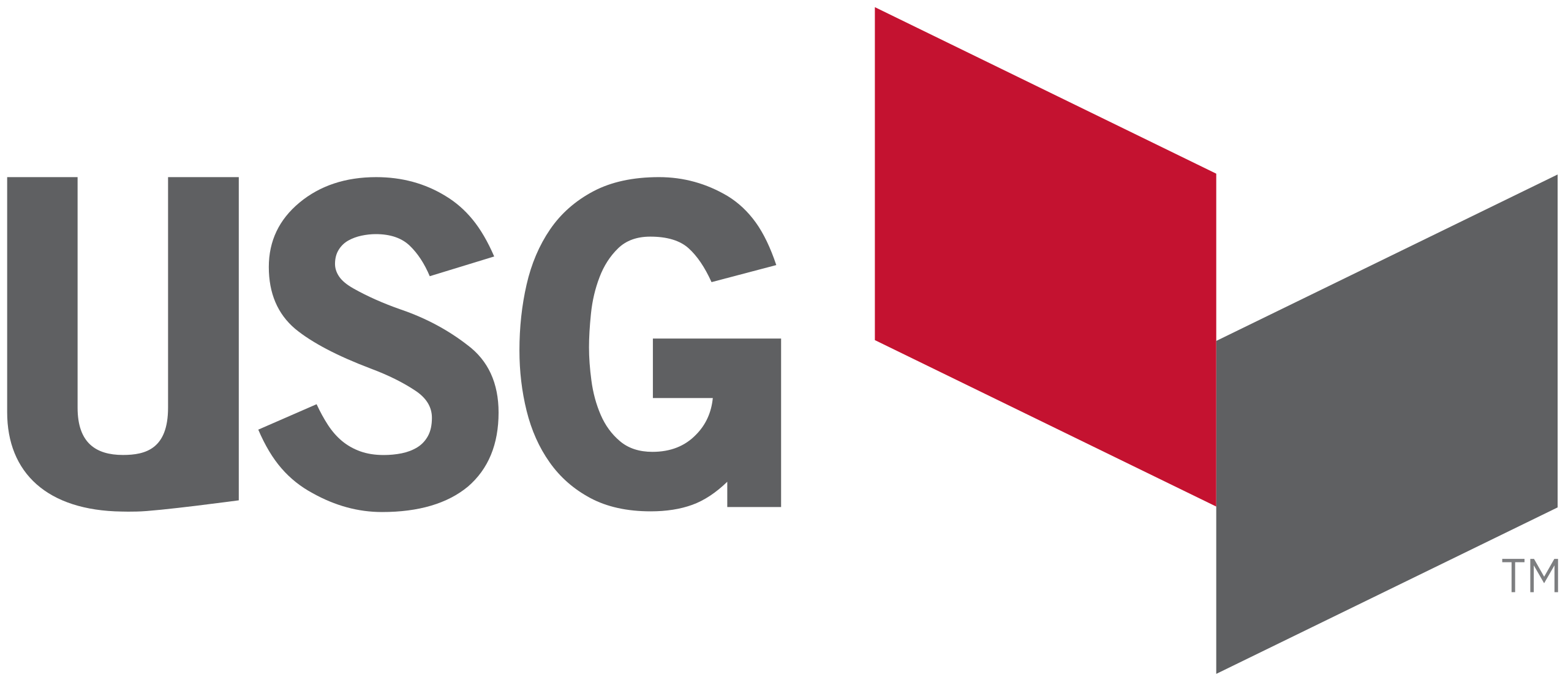
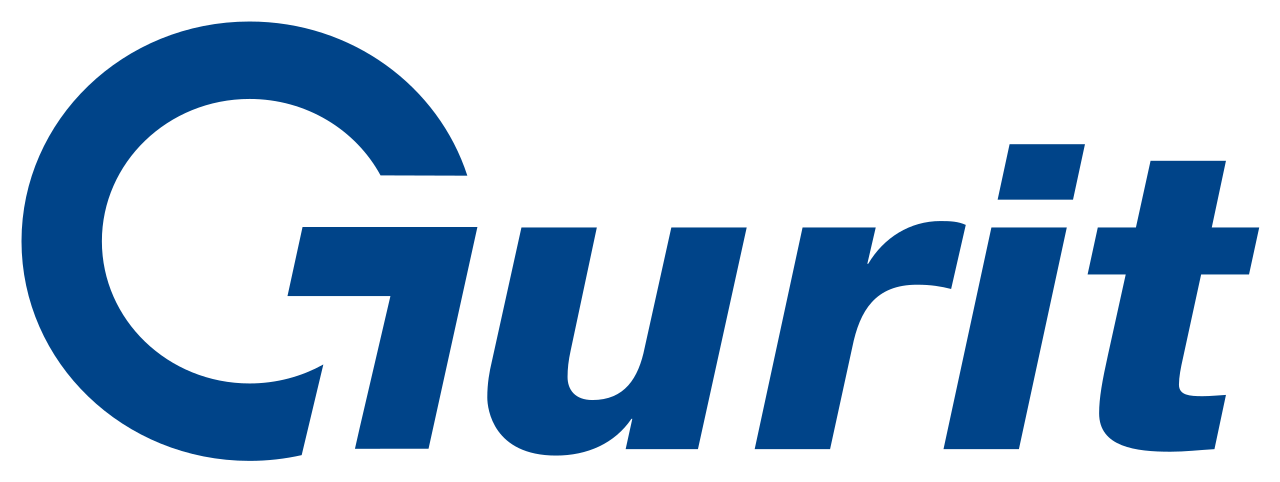
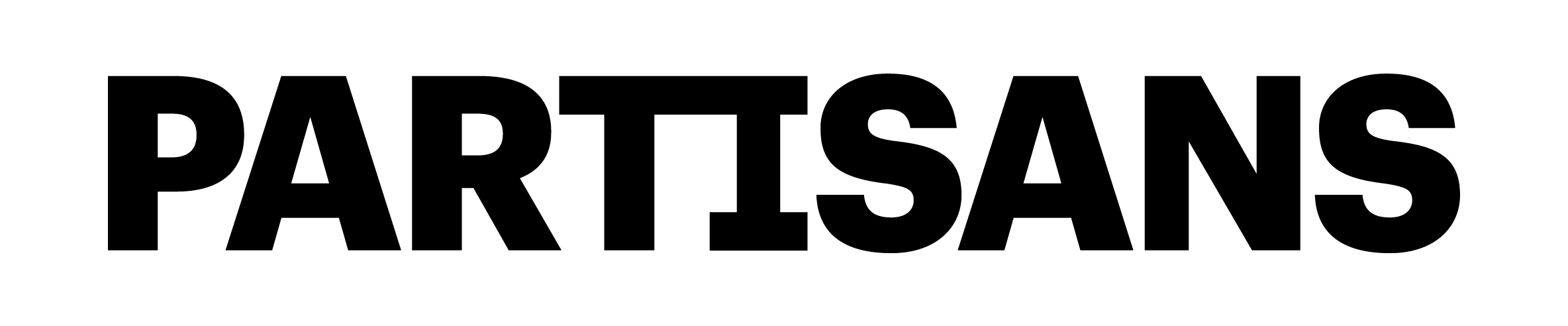

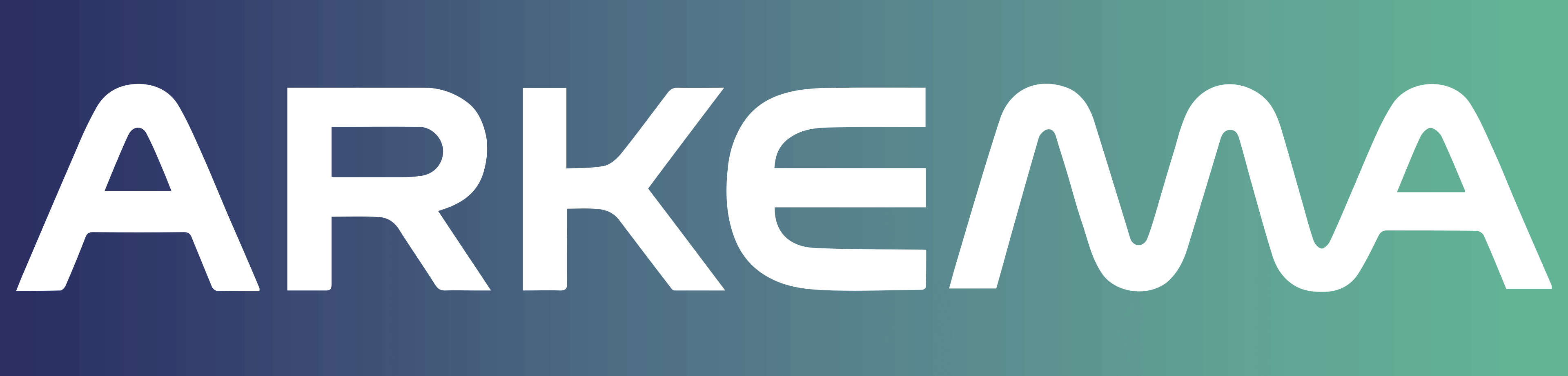
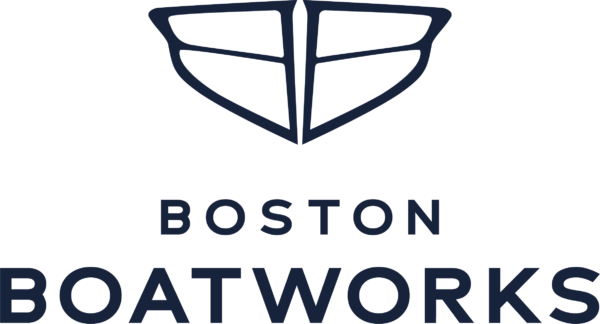
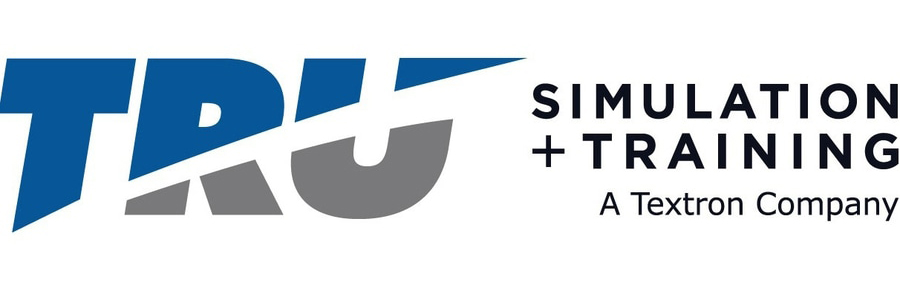
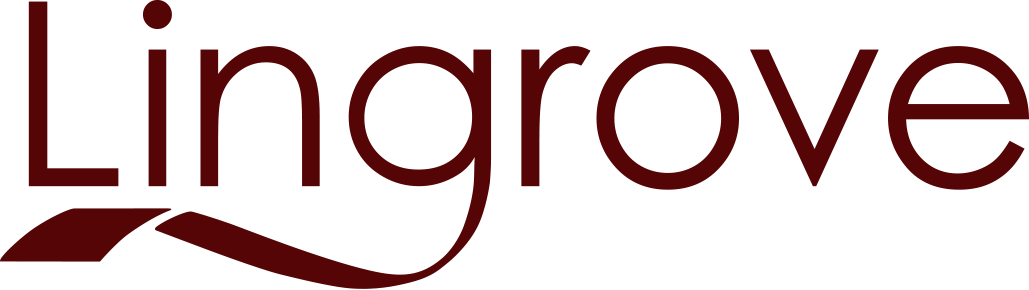
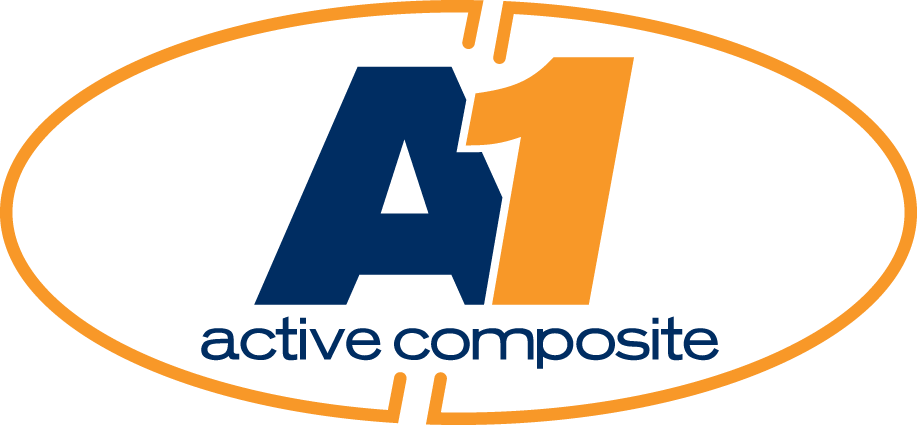
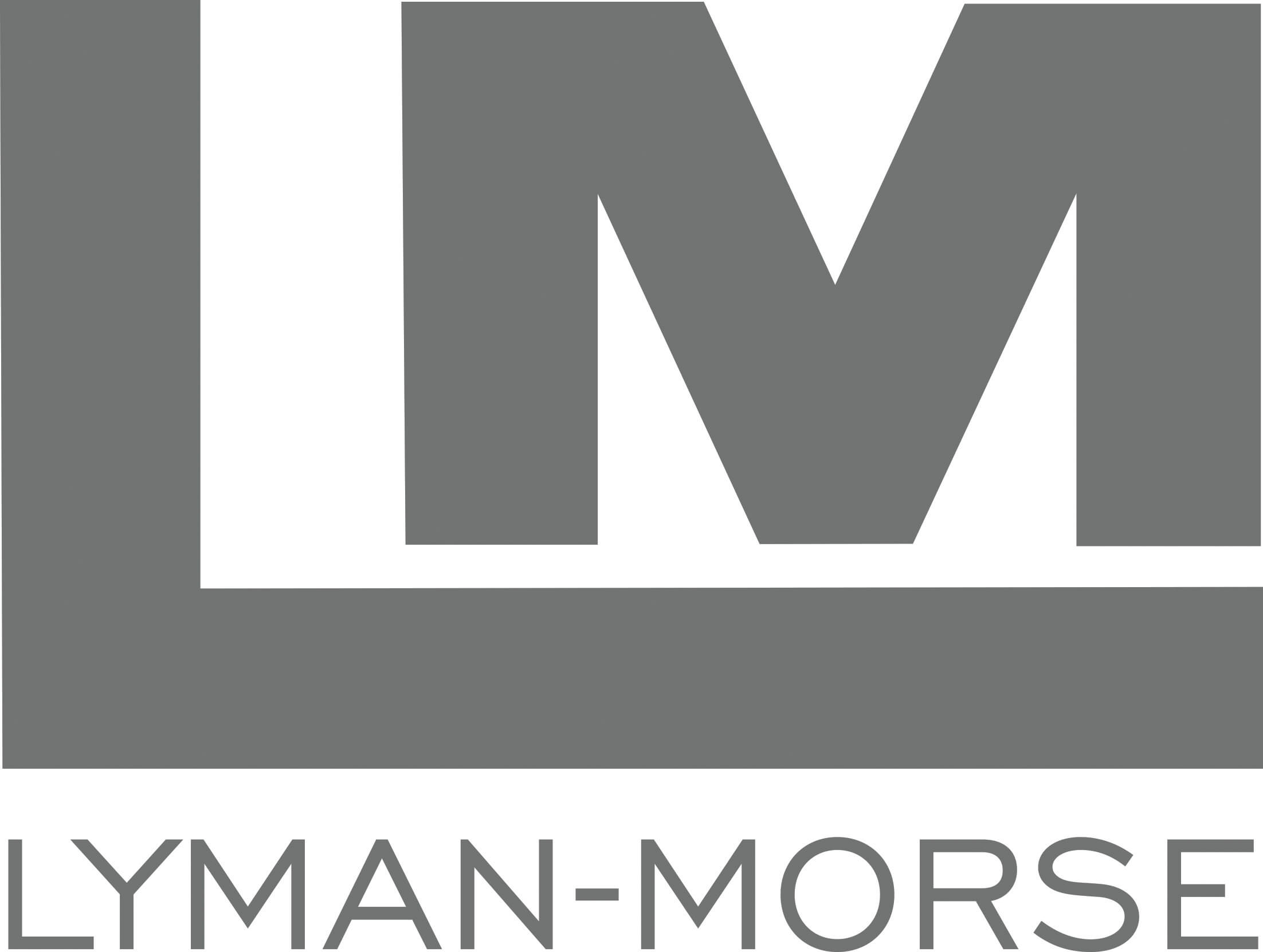
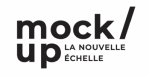
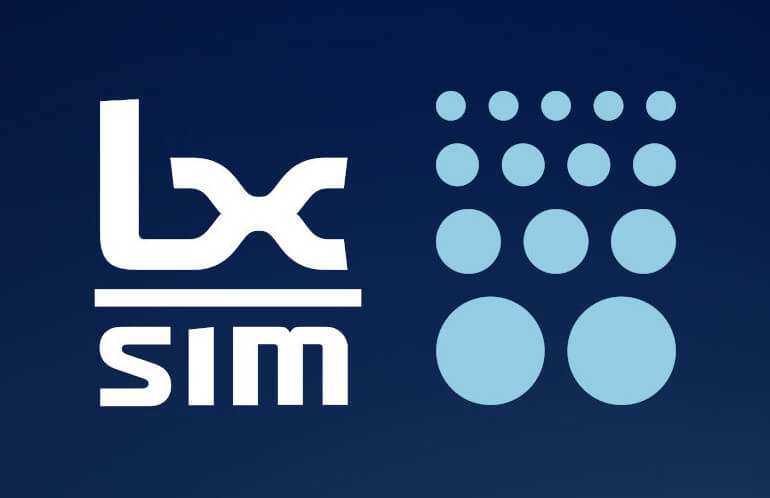
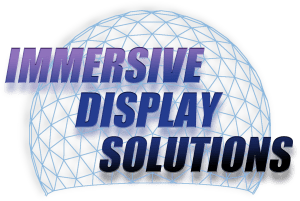
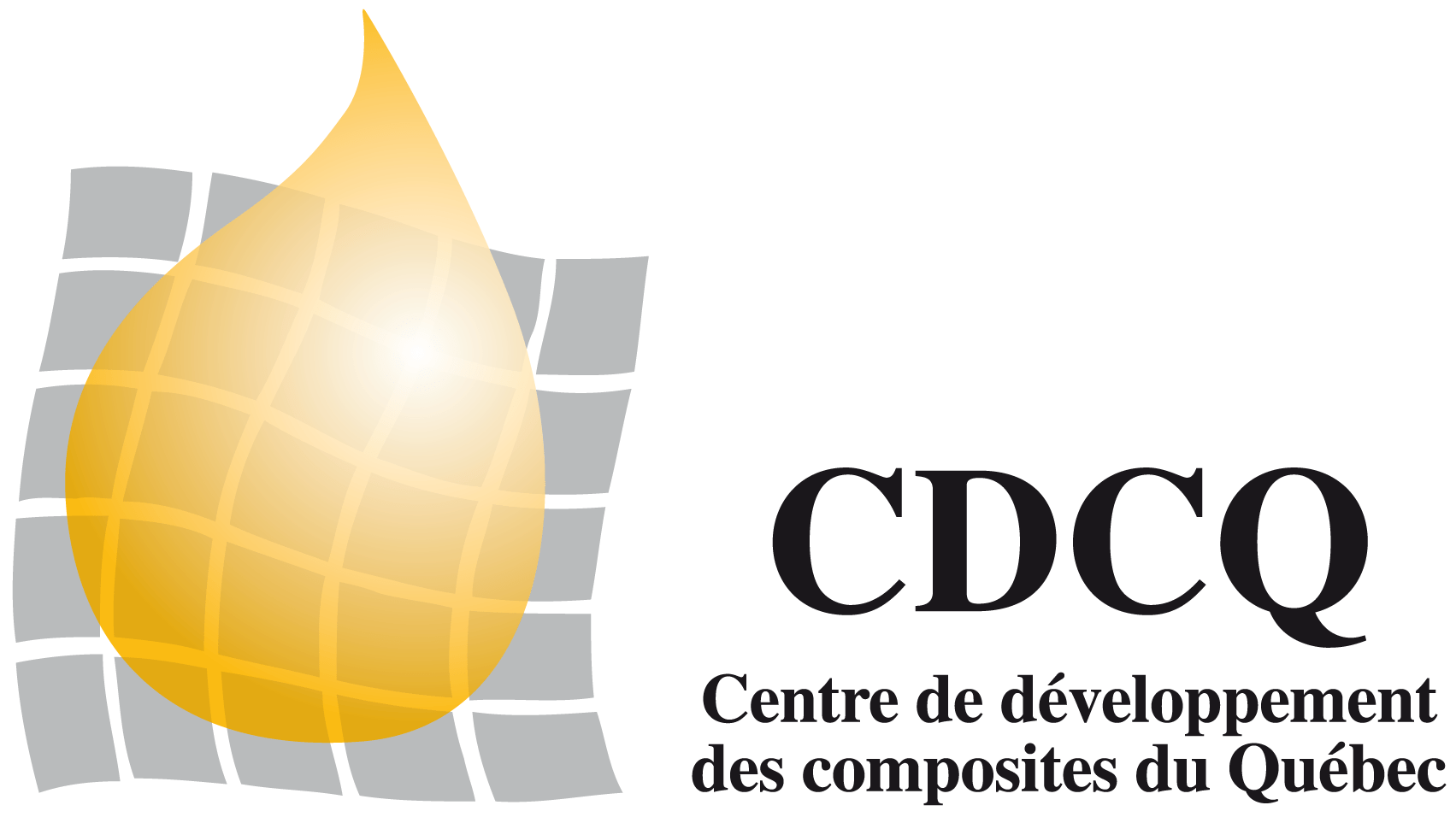
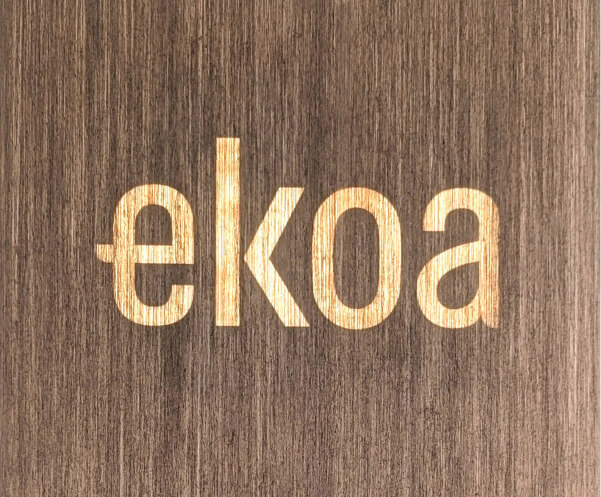
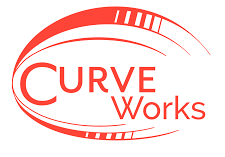
Our Commitment
Bespline eliminates waste and landfill from molds via a reconfigurable molding system that minimizes energy use and carbon footprint while developing bio-composites, recycled and recyclable material options for a uniquely sustainable alterative in composites manufacturing.
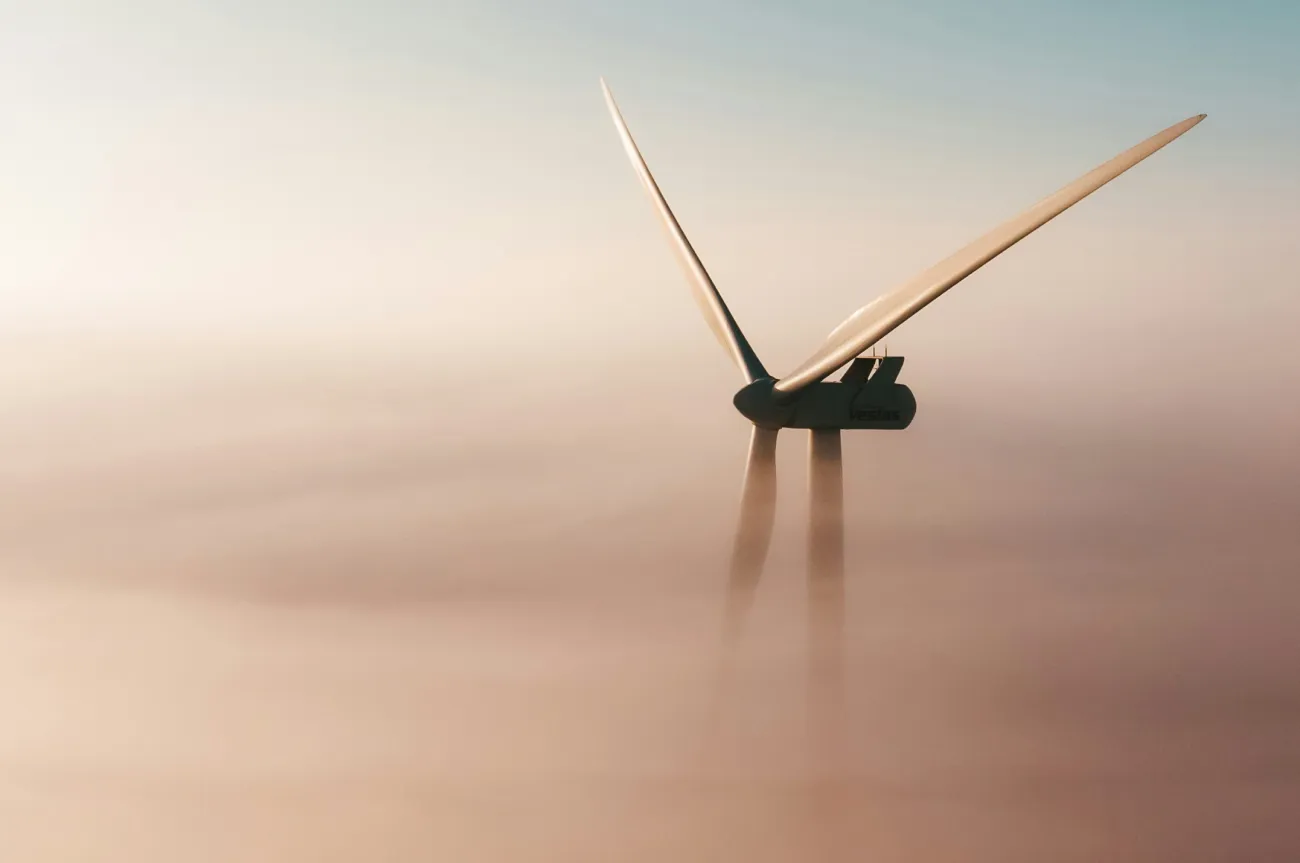
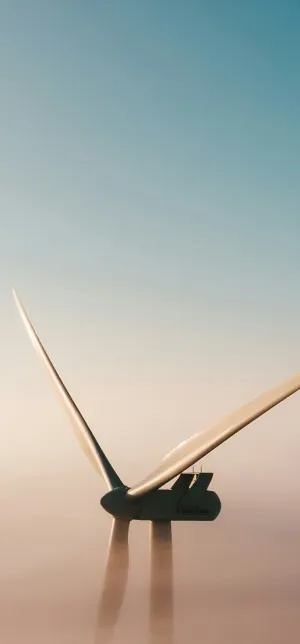